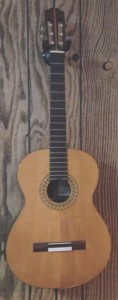
There are few issues more crucial to a luthier than managing workshop humidity. I learned this the hard way early in my career. One morning before sunrise as I sat sipping my first mug of coffee, I heard a very ominous sound. It wasn’t loud, but somehow I knew instantly what it was.
It was the sound of a crack occurring in the soundboard of my first guitar. Later I came to realize that horrifying event—arghhh, my first guitar!—was due to excessive humidity when I made it.
Relative humidity (in this article “RH,” or just “humidity”), unlike air temperature, can be very difficult to measure accurately and thus to manage. Since there are a number of ways to do these things, what follows will be: (1) the strategy I have settled on after decades of experience, and; (2) what I recommend to readers—not necessarily the same in all respects.
A good starting point for general knowledge for about RH for both luthiers and guitarists alike would be my article—recently updated in conjunction with this article—called “Humidity & Your Guitar’s Health.” If you’re a luthier and haven’t read that article yet, I’d suggest you do so and then come back here.
Measuring Humidity
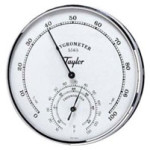
When my luthiery career began, there was no such thing as a digital hygrometer—in fact, no consumer-grade digital much-of-anything. The first mechanical hygrometers I tried were hopelessly inaccurate for a luthier’s workshop. Then I discovered the Taylor 5565 dial-type thermo-hygrometer, based on a hair-element sensor, and I have used this unit, several of them, ever since. They are accurate, dependable and calibratable, but they must be calibrated: the manufacturer’s calibrations vary by as much 5%.
So, how to calibrate them? I soon discovered the sling psychrometer (not to be confused with psychometer; that’s a term in psychology).

This device measures humidity based on a differential between a thermometer with a dry bulb and one with a bulb made wet by dipping the cotton sock that covers it in water. This video demonstrates the working principle of this tool.
A sling psychrometer is a very accurate way to measure humidity. The only problem is that it tends to measure 1%-2% higher—never lower—than true relative humidity. This is because the wet bulb ends up little short of maximum-cool when read by the operator.
Taking a reading with this device is also time consuming—and can be hard on the arm. You have to spend 2-3 minutes “slinging” the thing round and round, taking wet-bulb readings from time to time to see if the wet-bulb temperature has gone as low as it’s going to go and stabilized; then you have to immediately read and record the wet bulb temperature before it has a chance to start rising again, followed by a reading of the dry-bulb temperature. After that, you take your readings and consult a psychrometric chart…ooo, look at that thing, it’s really daunting, isn’t it. Fortunately there’s an easier way: a psychometric table. (I created that one over thirty years ago…on an electric typewriter.) You could also use a Bacharach Sling Psychrometer. That tool is equipped with a built-in slide-rule that calculates relative humidity for you. It also has a water reservoir for keeping the wick wet and folds up into a neat small bundle that fits inside a trousers pocket, which would make it ideal for field measurements outdoors; however, I find it somewhat cumbersome to use the slide-rule.
I’ve been providing myself quick and accurate humidity readings for decades by combining Taylor 5565’s (two in my workshop presently) with sling psychrometer readings to calibrate them. Once calibrated, the Taylor 5565’s seem to stay true indefinitely, at least as long as they’re kept in my workshop.
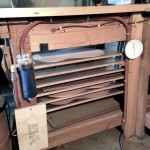
The most important thermo-hygrometer in my workshop is the one located near the climatizing rack. That’s where soundboards and backs are stored for several weeks before I complete them (bracing, shaping, etc.) and assemble them into guitar bodies. Those are the most crucial guitar components of all with regard to later humidity changes. Notice that there’s a thermo-hygrometer right next to the rack. (There’s also a ceiling fan directly above to keep air circulating around the rack constantly, and in the workshop generally.)
In recent times the technology of digital thermo-hygrometers has improved considerably. Although I plan to keep my psychrometer and dial-type equipment just because it works and it’s mine, I would counsel younger luthiers to go all-digital. Specifically, I would recommend—
-
Testo thermohygrometer One Testo 608-H1 thermo-hygrometer (cost ca $120). I have tested the one I own against other devices (digital & psychrometric) and concluded that it provides as much accuracy as can practically be achieved at a variety of humidity levels. The one-decimal-point feature is useless in absolute terms, but useful to get an indication as to whether the humidity level is changing, in what direction and how fast. I keep this unit close to my climatizing rack when a guitar is under construction.
-
Meade thermohygrometer Two Meade TM005X-M thermo-hygrometers (cost ca $20/ea) primarily for monitoring outdoor temperature/humidity. This unit comes with a wireless companion unit for monitoring outdoor conditions, which can be helpful for assessing your present indoor workshop climate needs. I would install the outdoor units on mountings a foot or so away from any structure if possible for free flow of outdoor air and in locations where one or the other is sheltered from precipitation but in the shade at any time of day/year. The outdoor units work best year-round when powered with lithium batteries. Compare the two indoor components with the Testo to see which one provides a humidity reading closest to the Testo (the Meade indoor units can vary in original calibration as much as 2%-3%); keep the most accurate one in the workshop as an alternative workshop unit, find a place in your residence for the other one.

One last note about humidity measuring devices: I equip the cases in which I deliver my own new guitars with a HygroSet II digital thermo-hygrometer, the only thermo-hygrometer I know of that’s calibratable by an ordinary user. They’re designed for monitoring humidity in cigar humidifiers, but they’re easy to install in the headstock compartment of any string instrument case. Calibrating one of these—using the Testo as a reference device—is a little tricky, but with some practice and patience it can be done.
Controlling Humidity Levels
The goal of a luthier in controlling humidity should be to get humidity to a level that creates an environment suitable for all stages of a string instrument construction, and to keep it there. This doesn’t mean that humidity must be kept at exactly the same level all the time; humidity is just too slippery and elusive to make that feasible. Rather, a reasonable goal is to maintain a range of humidity levels.
But what is that range? My experience has convinced me that the range should center around 45% RH. In my workshop, I long sought to maintain a year-round range of ±2% around that center. The control equipment I’ve developed to achieve that looks like this—
-
Regin HMH humidistat A Regin HMH humidistat with a long (17cm), high-precision hair-element sensor; this provides a differential of ±1.5%, which makes a very small humidity range possible. This device is bi-configurable for both a humidifier and dehumidifier by adding a separate 3-way switch (humidifier/off/dehumidifier).
- 24v electrical HVAC-type connections from the humidistat to the humidifier/dehumidifier, which entails the use of sheltered relays with transformers to convert 24v DC electrical current to the 120v AC required by the humidifier/dehumidifier. (I use similar 24v-based systems for workshop heating and air conditioning). This permits the use of mere wall-mounted thermostat wire to get from the signals from control devices to the humidifier/dehumidifier/air conditioner/heater, but the overall system is technically quite complex.
So, what do other luthiers need? The simple answer: not as much as I have. In my system, the Regin HMH humidistat alone will set you back about $500…if you can find one. A complete custom 24vDC->120vAC system like mine would probably cost you between $1k-$2k—that’s just a best guess—in cash outlay and countless hours spent designing and installing it.
More recently I have come to the conclusion that a humidity differential of 45% ±4% is probably satisfactory for a guitar maker’s workshop, …±5% marginal at either extreme. (That’s a far cry from what’s acceptable for a guitar owner, …±15%.) That addition of 2% at either end makes a big difference in what you’ll need equipment-wise to deal with humidity in your workshop.
Built-in controls in humidifiers and dehumidifiers, while acceptable for home use, are not adequate for a luthier’s workshop. They will not reliably maintain conditions that fall within the 45% ±4% range; the on/off cycle times are just too long…and humidity is too elusive.
I would recommend these controls for controlling humidity—
-
Dayton humidity controls Dehumidifier: Dayton 1UHG2 dehumidifier control. This device has an interrupter plug linked to a built-in humidistat with a very low differential. This will assure frequent dehumidifier cycling to maintain a healthy humidity range for guitar construction.
- Humidifier: Dayton 1UHG3 humidifier control. This device works on the same principle as the Dayton humidifier control, except that the current kicks in when humidity gets too low.
These controls should be located away from the devices they are controlling so they will respond as much as possible to overall workshop conditions. I would ignore the humidity display of these controls—it doesn’t seem to be very accurate—and rely on your trusted hygrometer; tweak the control’s adjustment dial until it produces the humidity range you need.
Humidifying & Dehumidifying
So, what does a luthier need today? One thing for sure: the workshop HVAC system, including humidity management, should be completely separate from the residence system if the two areas are part of the same structure, as are mine. If you don’t keep the systems separate, you’re inviting avoidable system management complexity in the workshop. It you have any residential vents in your workshop, I suggest you shut them.
Perhaps the best place to start is to tell you something about the outside weather conditions, and the way they affect humidity levels, where I reside and work. Here in the U. S. midwest, they are probably about as year-round extreme as any you’ll find on Earth. In the dead of winter—December-January—temperatures can reach zero degrees Fahrenheit or below on some nights; if I did nothing about humidity, it would plummet to 10%-15%. During the months of May-June—in 2015 continuing, most unusually, into early July—we can experience rainy weather alongside outside temperatures in the low-to-mid sixties. If I ignored humidity then, it would soar to 80%-90% in my workshop. That’s a potential 80% annual variance in humidity. Needless to say, this is not the world’s weather-friendliest location for a luthier, but it has taught me more than a few things about managing humidity.
In my location, excessive dryness is definitely the more daunting humidity management problem. Simple arithmetic makes the reason for this apparent. During the spring-summer-fall period, a tolerable inside-outside temperature differential during extremely hot weather might be 25° (75°-100°); at times like this, the air conditioner is already removing considerable excess water, leaving little burden for the dehumidifier. However, during extreme cold winter weather, the inside-outside temperature differential is much greater, as much as 70° (70°-0°), and there’s no collaboration between climate management devices as in the summer; you just have to add water to the air until you get the humidity right.
During times of humidity extremes, my practical goals nowadays for humidity maintenance change somewhat. When it’s rainy outside and the temperature is low-to-mid-sixties, I aim for >44%/<48%, very attainable with the dehumidifier I currently use (and will recommend). During winter cold snaps, I may on some days be aiming for >42%/<46%…actually during the very coldest of winter nights, I may not be eager to see the humidity go higher than about 42% in order to avoid excessive condensation on windows and in walls. This strategy permits me to do any and all tasks on a guitar, including body assembly, any day of the year. Here is how I currently go about this—
-
Honeywell TrueSTEAM 9-gal./day steam humidifier in my workshop Humidifier: Honeywell TrueSTEAM 9 gal./day with a Honeywell RO (reverse osmosis) filtration system to soften the water and reduce—indeed, virtually eliminate—mineral deposits. This device puts out enough humidity to cope with the most extreme dryness I have ever encountered. Since it’s designed for installation on a home furnace, it has its own 24vDC terminal, eliminating the need for a custom relay w/transformer. I use the Regin HMH humidistat in place of the one provided by Honeywell (called a HumidiPRO), but I would presume that the Honeywell humidistat would work adequately (I intend to test the HumidiPRO for accuracy but will have to wait for cold weather). My TrueSTEAM is mounted on a vertical board—instead of a duct— where the steam jet is well out of the way of harm from scalding. The TrueSTEAM unit itself can be configured for ductless operation—required for board-mounting like mine—by resetting an internal DIP switch.
- Dehumidifier: Fantech GD55S. I have gone through possibly as many as 7-8 dehumidifiers in my luthiery career—I’ve lost count—and this is the only one I have been enthusiastically satisfied with. When I purchased mine in 2008, it was sold under the original brand name “Wood’s” (W.C. Wood Co., Guelph, Ontario Canada). A representative of Fantech USA—the international company that purchased W.C. Wood Co.—has assured me that the unit currently being offered under that company’s name is identical to mine—the front panel still bears the “Wood’s” logo—and continues to be made in Canada. Its dehumidification capacity is more than enough to keep my workshop humidity within bounds under the most challenging conditions, and it does so with very little cast-off heat, which has been a major problem with condenser-type dehumidifiers I have used in the past. The current price tag on this unit is about $460, much less than I paid in 2008 for mine.
So what do you need to discipline humidity in your workshop? If you’ve read this far, by now it has surely dawned on you that it depends largely on where you’re located. If you’re in the U.S. Pacific northwest in a coastal area, your biggest challenge may be dehumidifying. On the other hand if you find yourself in Saskatchewan, Canada, winter humidifying may be your biggest problem. Maybe humidity at either extreme isn’t a problem where you’re located, in which case you could get by with lesser-capacity equipment than mine.
I am of a mixed mind about endorsing the Honeywell TrueSTEAM like the one in my workshop. Installation of one of these units is quite technical…normally it’s done by HVAC professionals. If tap water is used to create the steam, the residue and scaling that is an unavoidable aftereffect of unfiltered—or minimally filtered—boiling water can be problematic; that’s why I wouldn’t use one without the Honeywell RO filtration system. Unless you must deal with really extreme dryness, this type of humidifier is probably an overkill; there’s a simpler way that I will describe later.
I can only attest to my own experience: Both of the TrueSTEAM units I am currently using—workshop and home furnace—show no sign of scaling on water-immersed components and a thimbleful or less of powdery mineral deposits in a post-season inspection of the the water tank…following installation of Honeywell RO filtration systems for both units. There is an annual maintenance cost—filter replacements—for the RO system in addition to the startup cost of the basic equipment. RO filtration also consumes quite a bit of cast-off water in the filtering process; expect a small increase in your water bill when the TrueSTEAM is doing its work. The TrueSTEAM is a relatively expensive, complex humidity solution for a luthier.
However, if you’re confronted with extreme indoor dryness for a substantial part of a year, as I am, and need a heavy-duty moisture input to cope with this, I know of no other solution that’s the equal of a steam humidifier, and I’ve tried many. The unit I have permits me to set the desired humidity level and leave the issue unattended. An alternative to the TrueSTEAM might be the Aprilaire 800 steam humidifier, except that there appears to be no way to configure that unit internally, as with the TrueSTEAM, for ductless installation; an add-on device to adapt the unit for ductless use appears to be no longer available from Aprilaire.
Here’s another solution for dryness-defense that’s much simpler: an Essick Air evaporative humidifier. I recommend this specific brand/model because it’s the one I have the most experience with. In addition, I know it can be equipped with a float valve and plumbed to your main water supply, which eliminates the need for daily manual filling of water bottles. The operative principle of this device entails a wick inside the unit that draws water up into the path of a fan and out into your workshop as vapor. The water inside the unit needs to be treated for bacteria and dumped or drained occasionally to get rid of minerals left behind in the evaporation process. The inexpensive evaporation wick needs to be replaced when it becomes too encrusted with mineral deposits to absorb water effectively.
The limitations of the Essick Air unit—or any other evaporative humidifier—will be encountered in times of the most extreme dryness; at such times it will not keep workshop humidity up to the 42% minimum I recommend for guitar construction. In such conditions, one can add more humidity by using using a warm mist humidifier. Back when I was using my Essick Air humidifier (I still have that device, just in case…) I would deploy the warm mist humidifier at full steam during the coldest times of winter nights, letting the Essick Air control the humidity level via the Regin humidistat. If that combination of remedies proved insufficient on the very coldest nights, I would simply turn the workshop temperature down 5° overnight. Obviously that’s more trouble than letting the TrueSTEAM take full charge of humidity, which is why I made the change. On the other hand, if dryness in your location is more moderate than in mine, an Essick Air humidifier may be all you need.
As for dehumidifiers, little need be added to the previous reference to the Fantech unit. A note of caution, however, about water removal ratings: the Fantech unit I recommend, for example, advertises 101 pints of water removal daily…but that’s at 90% RH, which is the standard rubric for refrigerant-type dehumidifiers. The device will not remove anything close to that volume of water from your workshop environment in a day, but that’s OK as long as it will keep humidity under 48%. Some of the dehumidifiers I’ve tried down through the years—Including one “commercial” dehumidifier that I invested $1k+ in that was obnoxiously noisy to boot—would not always do that.
As I’ve been drawing this article to a close, it has occurred to me more and more that its contribution public luthiery knowledge might just be the details of how I have learned to deal with humidity in the very specific set of climate conditions where I work. Nothing would please me more than to see this effort of mine turn into a forum for contributions from other luthiers around the world who work in very different conditions. I invite comments.
Thanks Paul,
this is the best insight I have seen as to how to wrangle workshop humidity. Thanks for you effort on this.
We’re just about to set up our first sizeable, and serious, guitar making workshop and we’ll let you know our experience with climate control here in the Southern Highlands of NSW, Australia.
Cheers
Andy Thomson
T Guitars
Your Comment has prompted me to finally take action on an urgent update to this article. It will take the form of an addendum about steam humidification in very dry conditions. For now my advice to you is: DO NOT INSTALL A TRUESTEAM HUMIDIFIER in your workshop.
Please let us know what the issue is with the truestream humidifier
The TrueSTEAM humidifier requires RO (reverse osmosis) filtered water; without that, the heating coil and the sensors get caked with mineral scale. If you have moderately hard water, a simple inline filter will not do the job. (Present TrueSTEAM units are being being offered only with RO filters.) The problem I’ve run into with RO filtered water is that it removes all electro-conductivity from the water, which is necessary for the sensors to function. As a result, the water tank overflows and/or the overflow service light comes on. It’s possible the newer TrueSTEAM models have overcome this problem. However, when my TrueSTEAM failed, I decided not to take a chance: I replaced the TrueSTEAM with an Aprilaire 850 that comes with a fan pack to disperse the steam. I am much more satisfied with the Aprilaire on many accounts, not least of all that it actually maintains full workshop humidity in the most extreme weather conditions.
I am currently residing on a Carribean Island in the British West Indies.
It can be a down pour one moment and dry the next. Challenging conditions !
I’ve been thinking about this, and I wonder whether relative humidity is what matters – I think what matters to a guitar is absolute humidity.
Let me explain my reasoning; at a level of 45% RH, a temperature of 18C and a barometric pressure of 1000, one cubic meter of air contains 7 grams of water. At the same level of relative humidity, 45%, and barometric pressure, but at a temperature of 30C, one cubic metre of air contains 14 grams of water!
The wood of the guitar will thus be only half as moist at the same level of relative humidity, if the temperature drops from 30C to 18C.
I think THIS is what matters, what are your thoughts?
A luthier’s concern about humidity is whether current conditions will tend to remove humidity or add humidity to wooden parts of a guitar. The only meaningful concept in that regard is relative humidity. Absolute humidity may be meaningful in other circumstances (I can’t think of any where it would be), but not in a luthier’s workshop.